

- 加工ごとに発注業者を変えていませんか?
- 複数の加工が重なることで、工程が伸びることに困っていませんか?
- 発注業者が増えるごとに、コストがかかっていませんか?
- プレス加工(順送加工、単発加工、絞り加工)
- 精密板金加工(専用金型不要)
- 巻き加工(ウレタンロールベンディング機)
- 溶接加工(ロボット溶接(曲線溶接、直角溶接、波形溶接)、自動溶接(直線溶接)、手溶接(職人の手で、複雑な形状に対応する溶接)、スタッド溶接(ネジ立て溶接)、スポット溶接(点溶接)
- 磨き加工(精密バフ仕上げ(手作業バフ研磨)、ディスクグライダー仕上げ、ワイヤ仕上げ)
を社内で一貫製造できる体制を整えております。これは、今までのお客さまのご要望に、都度、お応えしてきた結果に他ならないのですが、今では当社最大の特長となっています。
これは、ひとつひとつの加工を他工場に任す工程とは比べものにならないほど、コストの削減と時間の短縮を実現することができます。(例えば、プレス加工と溶接加工をする場合、プレス加工しか行わない工場の場合、次の溶接加工をするためには、他の工場に製品を運び、加工しなくてはなりません。コスト/時間:増)
そのため、
板金もので、材料の在庫があれば、最短3日で、製品がお手元に届きます。
(精密板金翌日出荷プロジェクト 当日12時迄の発注で、翌日出荷)
新規プレス加工品(単発・順送加工)であれば、金型製作から納品まで、最短1ヶ月半で対応しています。
今まで、このような複数の金属加工を必要とされていた企業さまからは、
- 加工毎に、業者への発注手間がなくなった。
- 加工手順をこちらで考えて、業者ごとに手配していたが、加工手順を考えることから任せられる。
- 複数の加工で、納期を短縮する事が難しかったが、解決できた。
- 納期が短縮されただけでなく、コスト面も抑えることができた。
等のお言葉をいただいております。
また、これらの5つの金属加工の前後には、資材調達、各種組立、梱包までの一連作業を行う体制も整えております。

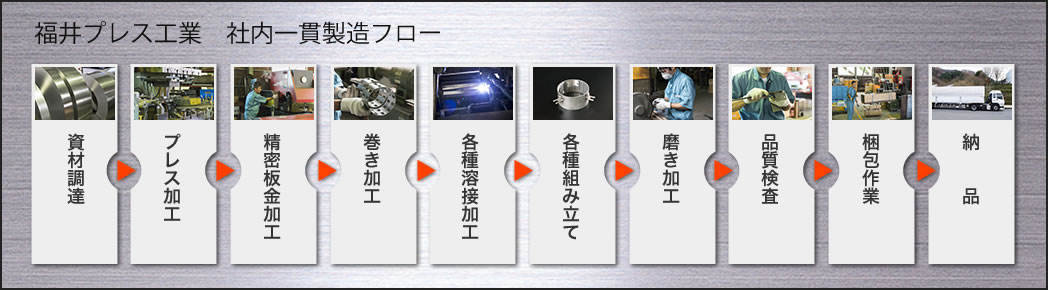
社内で複数の金属加工をおこなうため、意思の疎通を迅速にはかることは、とても重要です。そのために社内はオープンスペース体制をとり、いわば空白になりがちな加工間の溝が生じないよう、お互いの役割を把握するように努めています。作業効率の向上とともに他工程の内容を把握することができ、問題が発生した時には、前後の調整まで瞬時に行える体制を整えています。
そして、最大の利点としまして、さまざまな金属加工ができることから、ご依頼いただいたお客様に最適な工程の組み方をご提案させていただいております。技術者同士が知恵を出し合い、数分でも数時間でも効率よく生産できる加工方法を探しだし、短納期を実現しています。

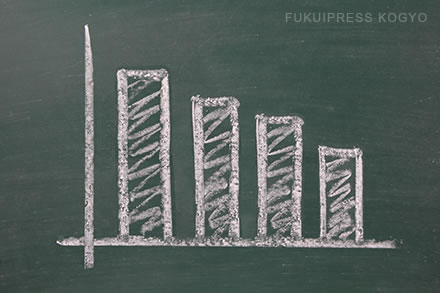
プレス加工ひとつとっても、金型ひとつを決めるまでには入念なやりとりを行います。どのようにすれば効率的に品質を高めた製品をつくることができるのかを念頭に置き、設計図を入念に調べ、機械とのバランス、作業性、材料との兼ね合いなど検討します。これら総合的な検討は、余分な作業一つ一つを削ることとなり、作業工数を減らし、労働作業のコスト削減にもつながっています。特にプレス加工(順送加工)の場合には、この総合的な検討如何によって、結果(作業時間、コスト)には大きな差が生じます。
特に、金属加工が複数の加工にまたがる場合は尚更です。ひとつひとつの金属加工だけでもさまざまな検討事項がありますが、さらに複合的に考えることが必要になると、その差はとてつもなく大きくなるからです。逆に言えば、複合的に金属加工作業の工程を考えられることで、ひとつの工程だけでは考えられなかった作業工程の見直し(減数や手順など)を考えだせることが容易になるということです。
そして、こうした取り組みを当社は、直にお客さまのコストへと反映させていただいております。お客さまの喜びと高効率化を目指す当社にとって、常に挑戦、常に技術力を高めるために、どんな小さなことでも大切にしています。

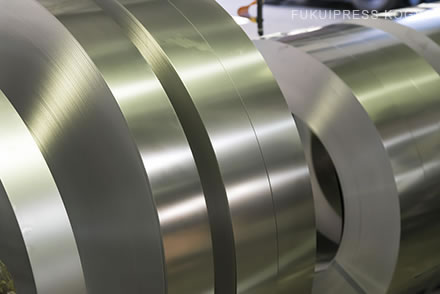
ステンレス材 SUS304, SUS430/神鋼(真鍮・銅)C2801P, C1100P/
純アルミ・アルミ合金 A5052P, A6063 等/鋼板 SPHC, SPCC/メッキ鋼鈑 SECC(ボンデ・ペンタイト), SGCC, ZAM,
【材料支給にて、金属加工可能な材料】
塩化ビニル